General Precautions
Thermal fuses shall be installed at the readily detectable location when abnormal conditions such as thermostat failure, fan failure, locked rotor, dry operation, etc., occurred in electronic appliance.Thermal fuses are designed to minimize the heat created from thermal fuses itself and maximize the detection of ambient temperature, but they may malfunction without detecting the temperature properly due to wrong installation. In order to minimize such malfunction, it is recommended to minimize the creation of heat around the thermal fuse in normal operating conditions, while maximize the heat generation in abnormal conditions. Followings shows conditions to comply for correct operation.
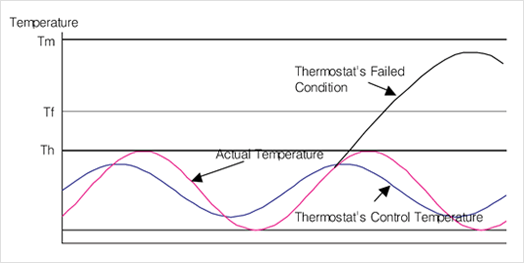
- · Each thermal fuse must be used within its own rated current and voltage, functioning temperature (TF),
holding temperature (TH), and maximum temperature (TM).
- · Thermal fuse connection shall be selected at a place where the undue stress due to vibration or other
displacement of parts in the completed product does not apply.
- · Thermal fuses shall be the installed at the place where the temperature is not increase above the highest service
temperature after the cutoff.
- · It cannot be used inside liquid or devices for which above 95% humidity need to be maintained.
- · Thermal fuses shall be installed a place where it detects only the intended heat source. If it is structurally inevitable,
a thermal shelter needs to be installed. For example, in a heater, thermal fuses shall not be connected directly
to heater to avoid the heat wire heats the thermal fuse directly.
- · Thermal fuses cannot be used in parallel connection or being exposed to continuous overload current and voltage
to improve current capacity, because such conditions may cause damage on inner joint and impact on normal
operation.
- Although thermal fuses are designed with high reliability, there is limitation in dealing with abnormal state with one thermal fuse. Furthermore, if the thermal fuse is damaged by man-made or unexpected uncontrollable act and out of work, the circuit braking is not working properly upon abnormal state in the device. Therefore, 2 or more thermal fuses having different functioning temperature have to be used if safety is highly required, when overheating or malfunction in a device may cause impact on the human body or there is no other circuit breaker except a fuse.
Lead Wire Forming
Copper lead wire is easy to bend, but it is likely to be damaged or broken if the lead wire is bent over right angle or bent repeatedly. Therefore keep in mind followings not to cause ant damage on the fuse.
- Forming molded lead wire
- Bend the lead wire at least 4 mm away from the molding. Otherwise, the damage of the molding worsens the air-tightness and impedes the normal operation of the thermal fuse. Use a nipper or other tools to prevent damage./dd>
- Forming unmolded lead wire
- Bend lead wire at least 4 mm away from the fuse body not to cause any damage.
- Use a jig or a radio-pincer in bending lead wire, and make sure not to make any cutting, denting, or crack.
Precaution for Connecting External Line to Lead Wire
- Make sure there is no crack or damage on the molded area or body of thermal fuses.
- If there is such damage as above, do not use it. Experimental assembly trials should be made to check the damage on the lead wire, molding or thermal fuse body.
- When connecting a wire to a thermal fuse, it is recommended to use a splice or a terminal.
- When securing a splice or a terminal, connecting tensile force needs to be 5 kg or higher so that impacts on the fuse can be minimized. Also, make sure not to cause overheating due to poor connection, use a splice or a terminal with low resistance so as not to cause abnormal temperature increase, and make sure not to cause any damage on the body during connection.
- Make sure the length of connection line to the fuse not over 50 cm, and it is better to use resistant wire.
- Recommended wire conductor is AWG 18 or 20. It is better to use flexible connecting wire, and use a stranded cable, if possible. To use single wire, bend it appropriately beforehand. (The longer wire length causes the more resistance, which raises heat on the fuse and may shorten the life.)
Soldering of Lead Wire
- Conduct soldering work on lead far from the thermal fuse, if possible.
- Minimize the heat transfer to thermal fuse body during soldering. Otherwise, molding or body of the thermal fuse may be damaged and inner circuit broken-down.
- To reduce the working time, employ pre-soldering process at the intended soldering area.
- Minimize heat transfer by holding lead wire around the thermal fuse with a nipper or other tool that can absolve the heat during soldering, and do not apply the heat more than 3 seconds.
- Otherwise, molding or body of the thermal fuse may be damaged and inner circuit would be broken-down.
Therefore, visual inspection, pre & post comparative resistance test and conductivity test, X-ray inspection, and operational check for the sample are recommended after soldering.
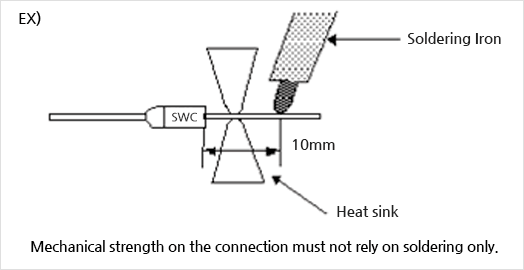
Electric Welding
Make sure that current for electric welding is not pass through the case of thermal fuse and cause damage during welding.
Molding
Note that molding can be damaged by boiling water, organic matters, or acid liquid.
Mechanical Strength
Do not apply 2 kg or higher tensile strength or 0.5 kg or higher compressive force on the lead wire. Also, do no apply excessive force or impact on the body. Note that thermal fuse damaged by impact may not work.